3-2-1: Modular Construction Driving Affordability, An All-Brick Development, Two Weeks Of Progress At 501 Main, & More
Issue #26
Happy Tuesday -
Here are 3 things from others, 2 things from me, and 1 picture related to incremental real estate development and my projects at Village Ventures.
Enjoy!
THREE THINGS FROM OTHERS
I. Modular Construction Driving Affordability
After construction of seven of the Harrison Row 40-unit townhome development in Chicago took eight months to complete, Structured Development turned to modular construction to expedite the process and drive down costs for the remaining 33.
By partnering with Kinexx Modular Construction, the developer was able to price each townhome around $245,000. Compare that to the $315,000 average home price across the city.
Modular construction moves the traditional process of building from on-site to remotely in a factory. Projects are built in sections in a controlled environment (i.e. warehouse)—complete with framing, electrical, mechanicals, plumbing, drywall, and finishes—before being transported to the site and installed.
This allows the construction process to avoid delays caused by bad weather (as I write this, we had to call off work on 501 Main due to rain). Each day a project is delayed costs money—construction debt service, property taxes, insurance, equipment rentals, etc—known as holding costs.
In addition, Structured Development partnered with a local, aspiring development group to build one of the townhomes and learn as they go. Such a great way to give back and introduce an educational component into a traditionally opaque process.
II. A Modern All-Brick Development

Carlton Landing is a New Urbanist town founded in 2008 by Jen and Grant Humphreys with a master plan for 3,000 homes and town center. It is located on Lake Eufaula in Oklahoma.
Carlton Landing is known for award-winning architecture and attracts some innovative builders and thinkers when it comes to design.
Clay Chapman is one of those innovators—a builder, designer, and mason with a goal of creating structures that last 1,000 years.
The Borough is Clay’s latest project—a collection of eight brick homes established as a micro-village. That’s structural brick, with the walls being three layers thick.
The residences are situated in a horseshoe shape around 4,000 SF of communal gathering space with a fire pit. This, along with the New Urbanist setting, enables an exceptionally walkable and community-oriented place to live.
Built in 2019, the homes were priced in the range of $260 per SF. Despite stunning architecture, details, and heavy reliance on masonry, Clay thinks he can eventually get down to $100 per SF in build costs.
III. Building Small: The Forum
I had the pleasure of connecting recently with Jim Heid—the developer behind the 12-unit River House project in Healdsburg, CA I wrote about earlier this year.
Jim is a seasoned real estate professional and advocate for small-scale development (in fact, he wrote a book called Building Small: A Toolkit for Real Estate Entrepreneurs, Civic Leaders, and Great Communities).
Twice a year, Jim organizes Building Small: The Forums, a mini conference focused on bringing together developers, policy makers, and capital providers. Each in a different location with evidence of small-scale development. Attendance is capped at 60 people.
This May will bring the 17th forum to San Antonio. For those of you interested in small-scale development (all of you I hope!), here’s a link for more info. Tickets are discounted until the end of the month.
TWO THINGS FROM ME
I. Project Updates—501 Main
It’s been a few weeks since I last posted on 501 Main. Not for lack of things to share—we’ve seen the most progress on the project to date.
Two weeks ago, two experienced carpenters started with me full-time. With the building demolished (see last post for details), we had our work cut out for us before we could start framing up.
This included:
Leveling and squaring the existing ground floor system
Installing a variety of hold downs fastened into the concrete specified by the engineer
Installing new carrying beams, joists, and hangers
Excavating, building forms, and pouring concrete for new piers, bulkhead, and frost wall
Here’s a quick photo walkthrough on progress.

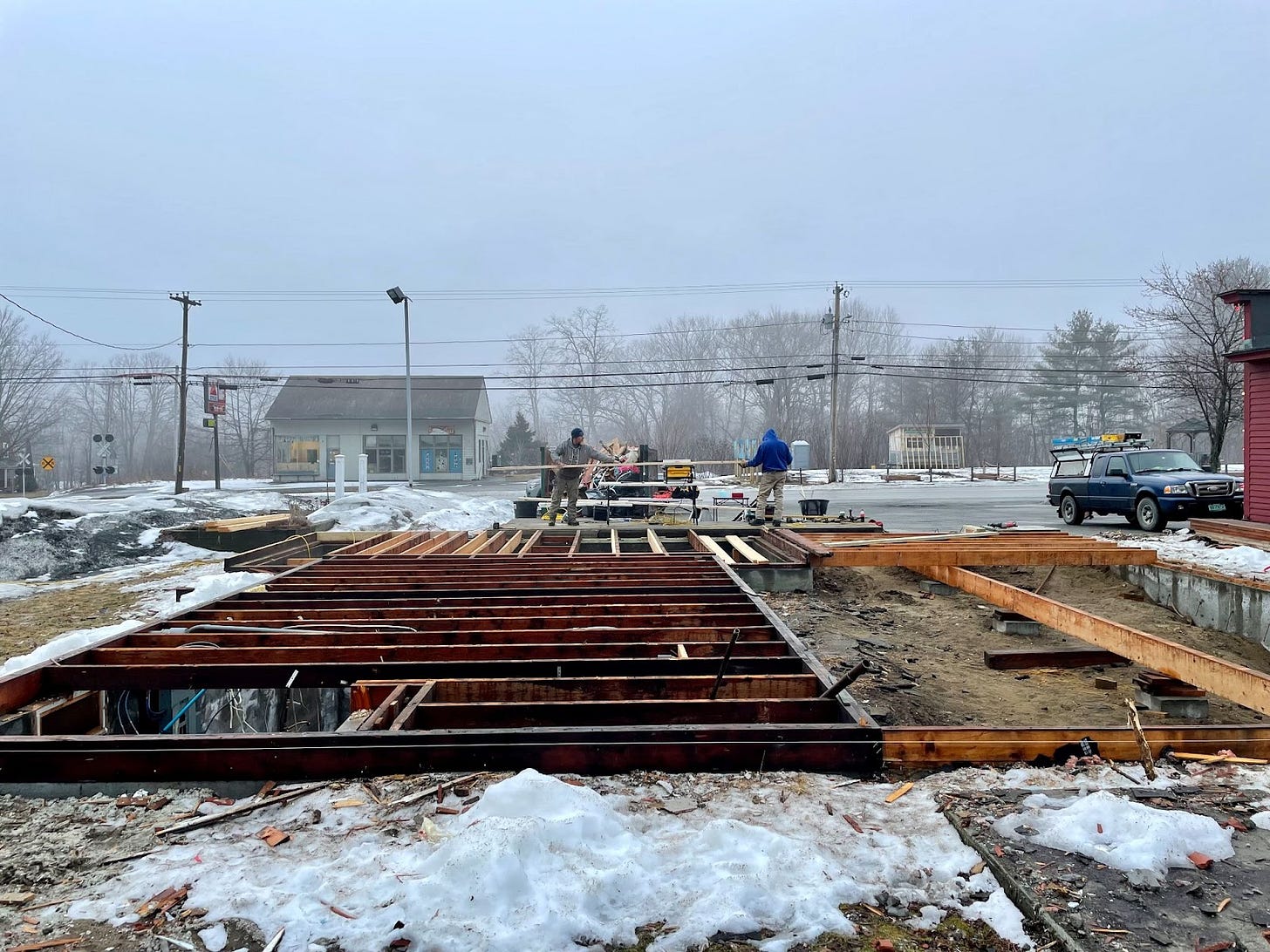
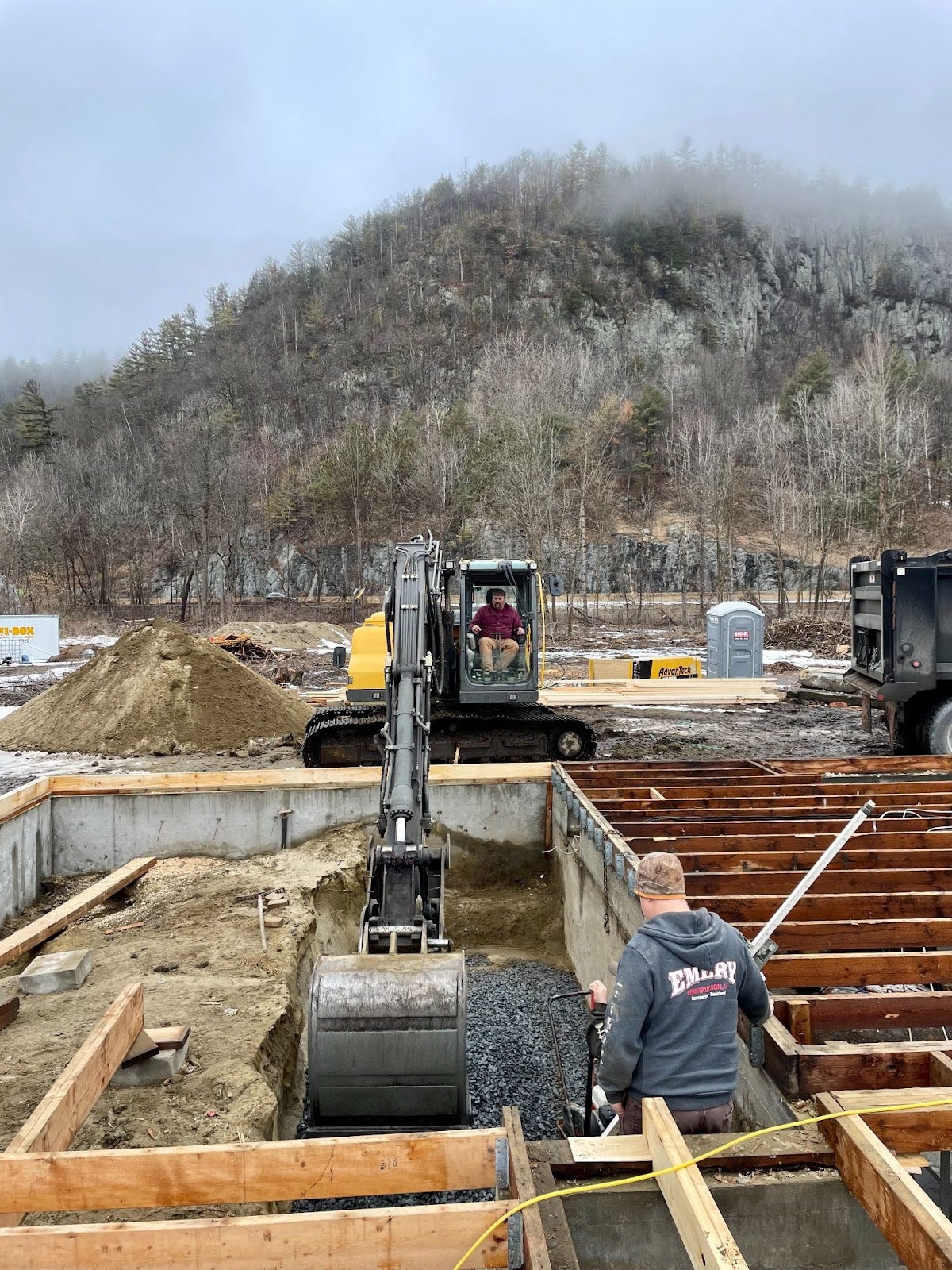
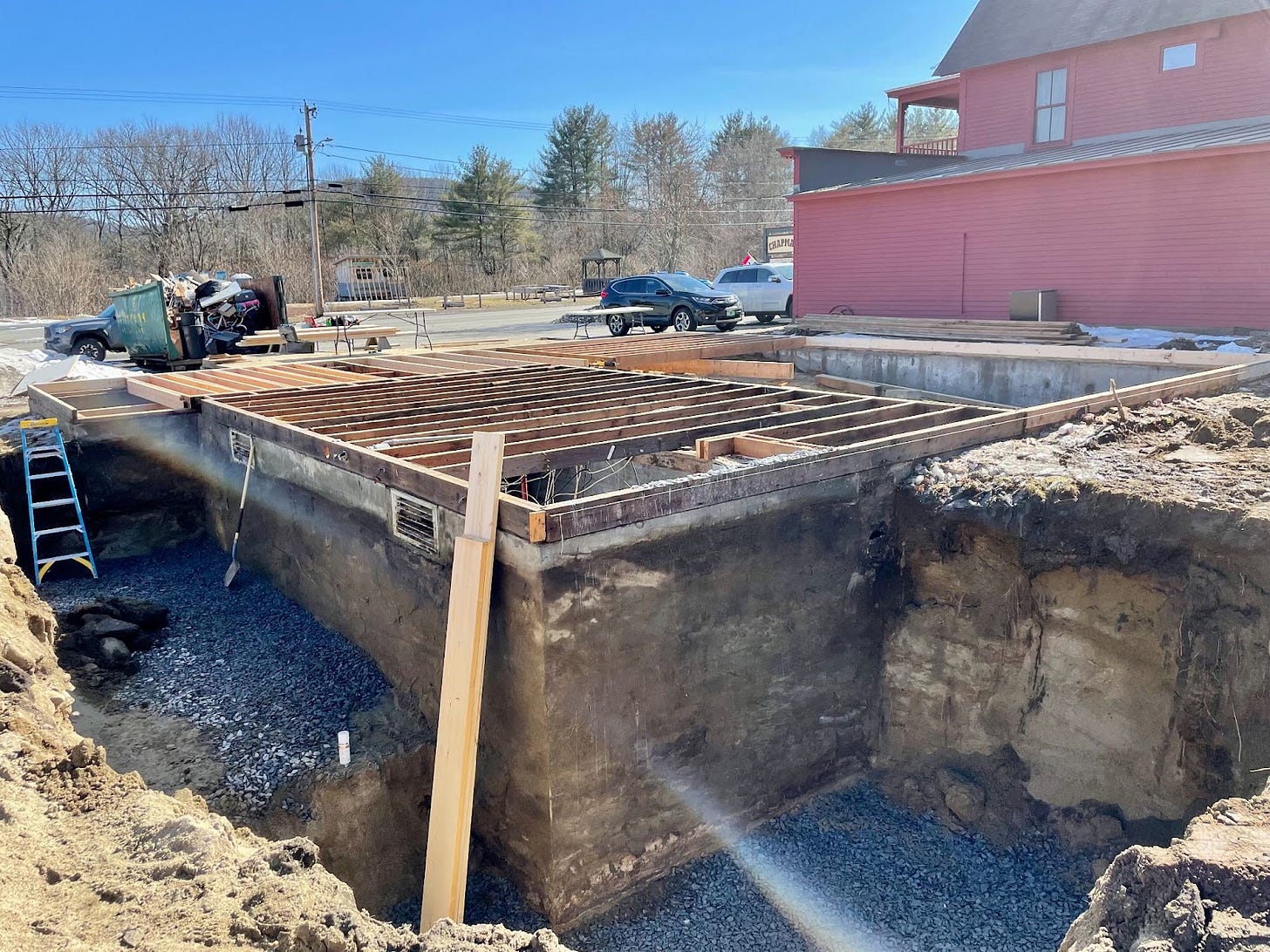
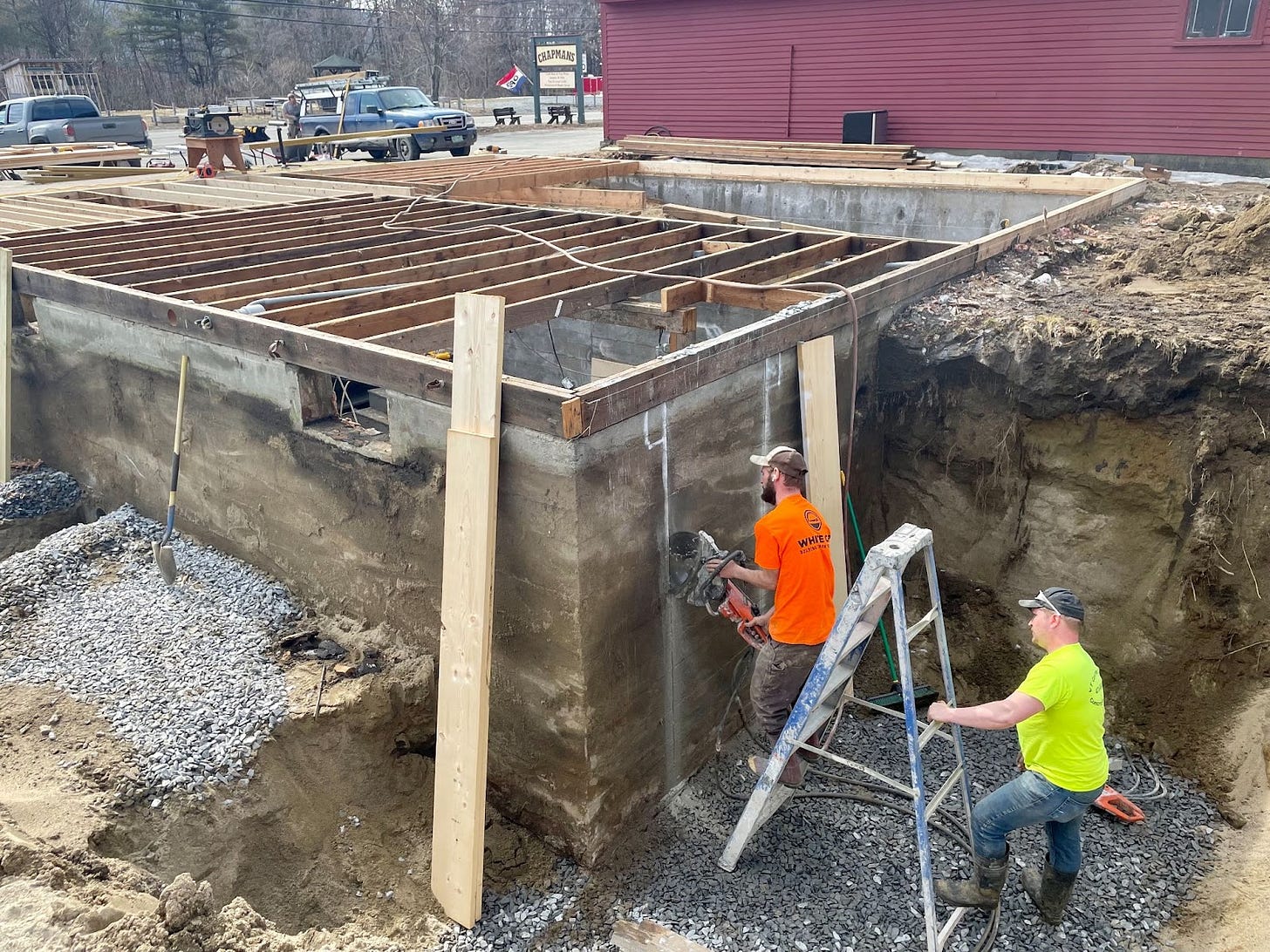

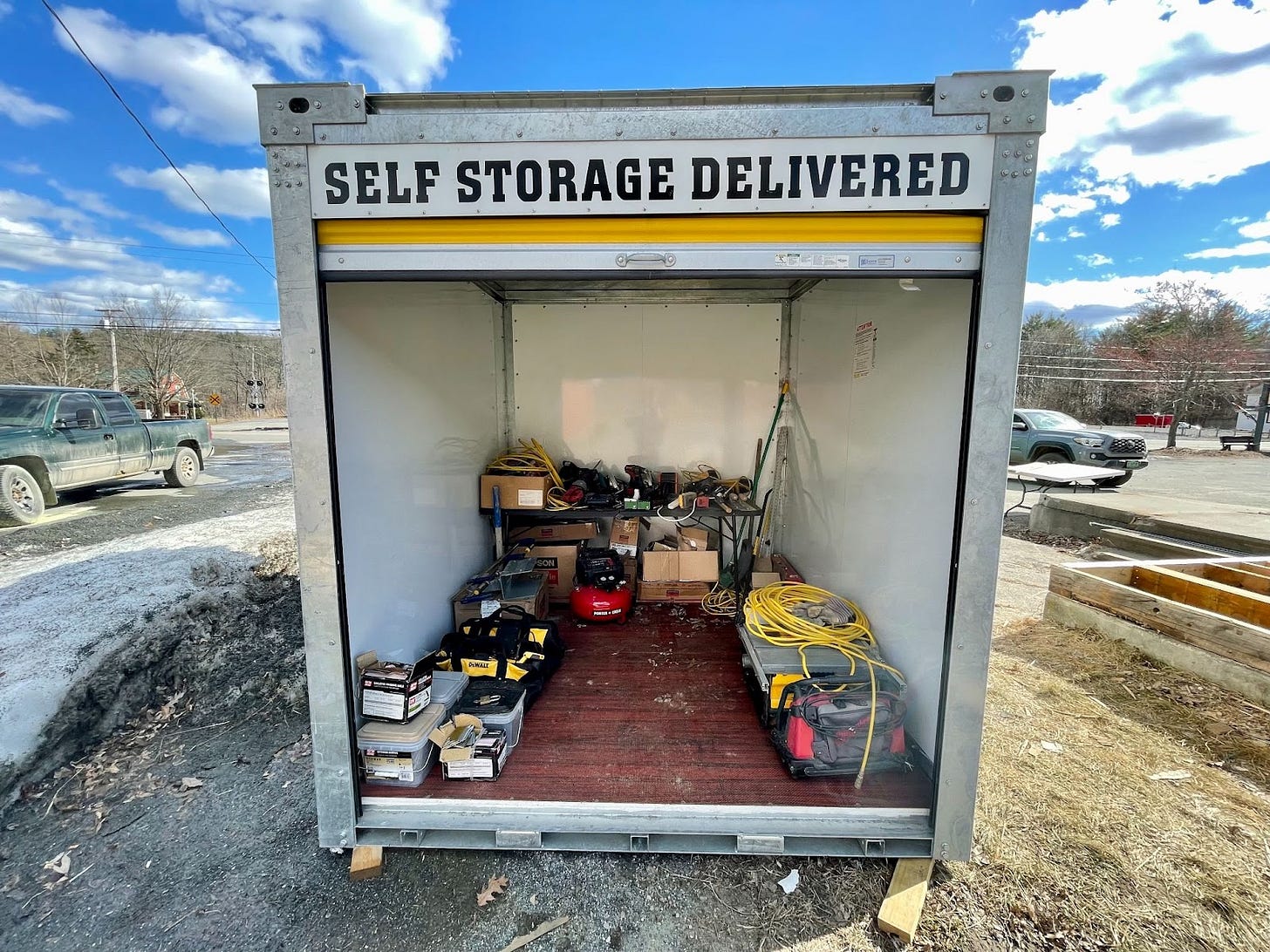
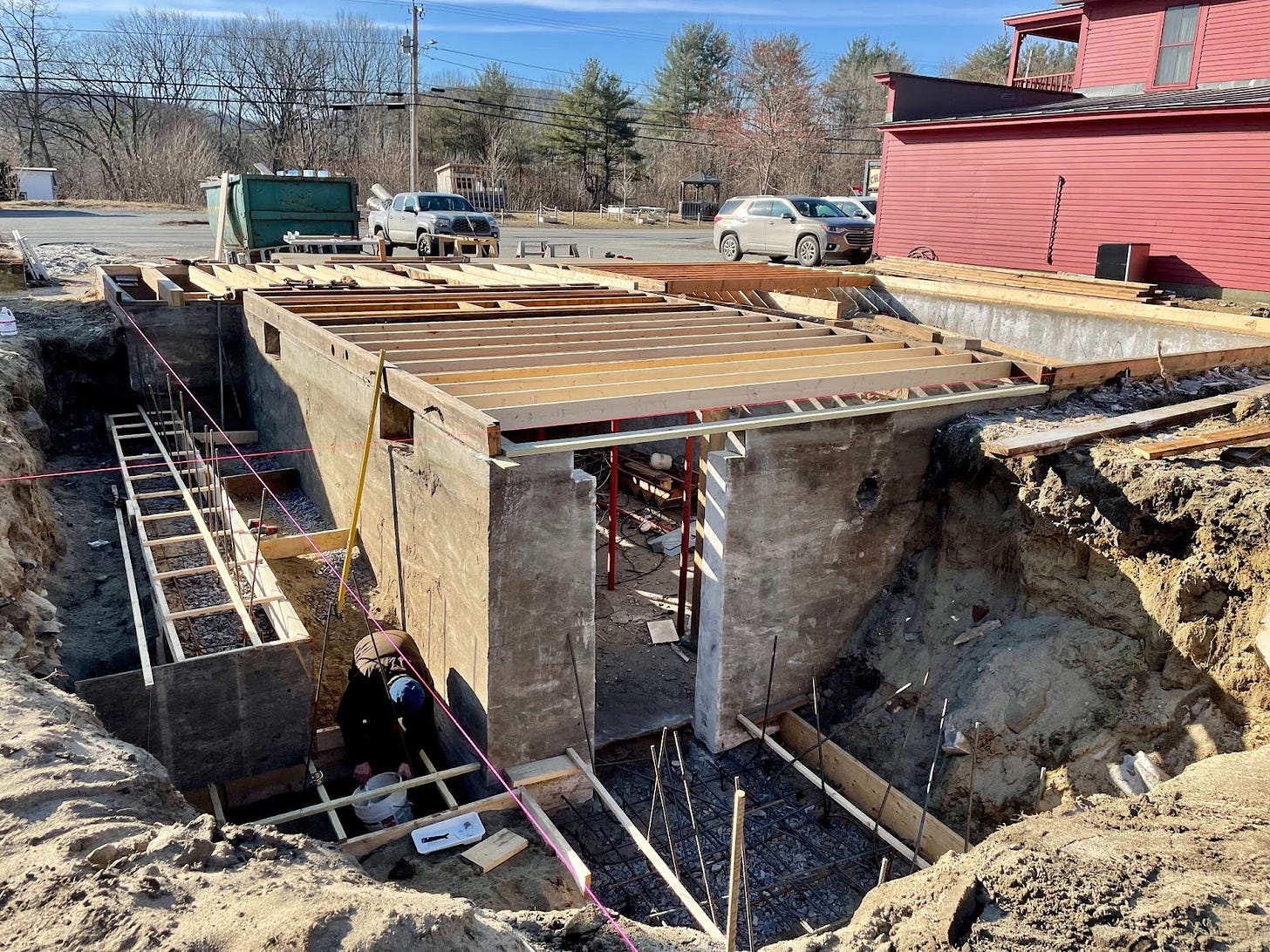
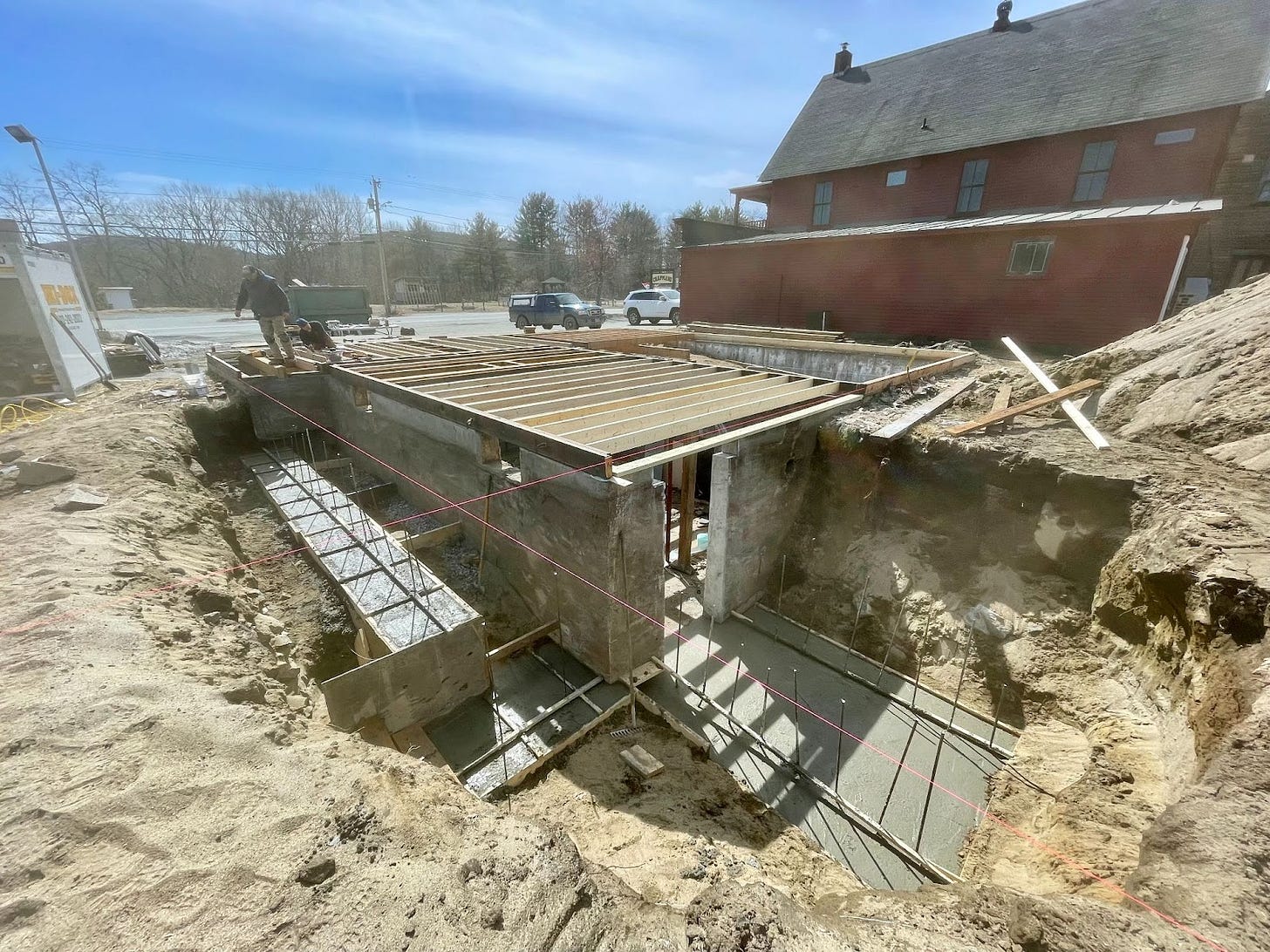
II. Our First Major Construction Miss
We had our first major construction miss last week at 501 Main.
The architectural and structural plans call for a bulkhead extending six feet from the foundation wall to access the basement of the building. Circled below.
We brought the site contractor out last week with his excavator to dig the area for the bulkhead, new frost wall, and interior piers.
We dug the bulkhead area a bit larger—nine feet long instead of six—just to be safe.
Well, it turns out that the extra 3’ didn’t cut it.
After we built forms and laid rebar (see below), it dawned on us that a 9’-long staircase might be steeper than code allows. After running the numbers on tread depth and riser height, the framers confirmed this.
We would need an additional 3’ to get a code-compliant staircase. That means further excavation extending perpendicular from the foundation. And additional formwork.
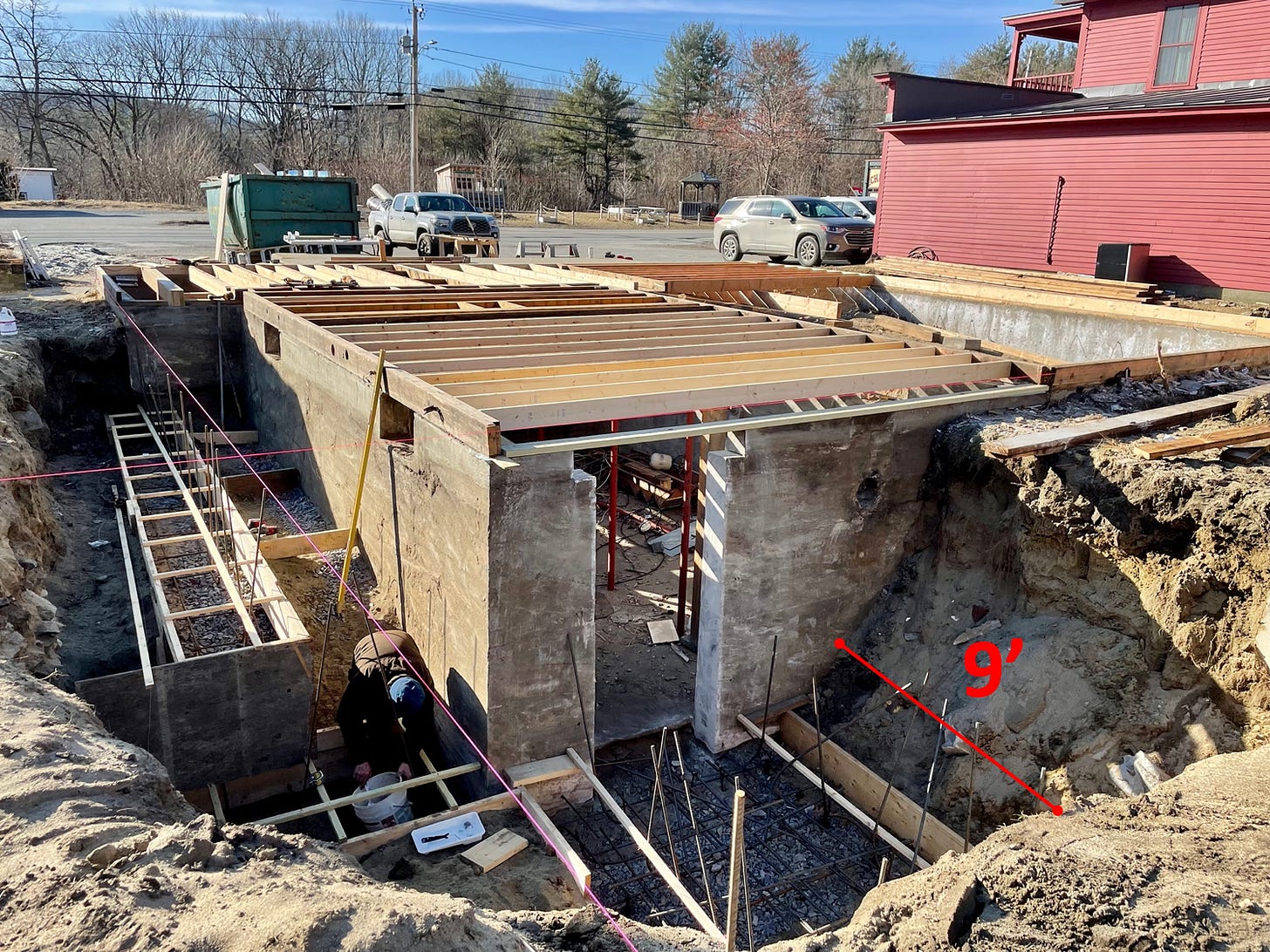
The architects then affirmed this. But, at this point, we were already scheduled to pour concrete the following day. So, we had a couple options:
Cancel pouring of bulkhead slab until we had a chance to excavate the additional 3’, build new forms, and lay rebar
Push forward as initially planned and add the extra 3’ of slab later
A couple considerations at play:
The walls of the excavated area were starting to collapse. It became a morning ritual to dig out the dirt that had fallen into our forms the night before. The longer we waited, the more we risked a full collapse
Every day spent in limbo costs money. Perhaps no labor costs, but there are still holding costs for insurance, debt, property taxes, etc. The faster a project is completed and leased up, the less holding costs incurred
The new frost wall is critical to begin framing the first floor. The bulkhead is not. It is priority getting that frost wall completed so that the framers can start building up
As you might have guessed from the earlier pictures, we pushed forward with path #2 and poured what we could, including what we had formed for the bulkhead slab.
We’ll ultimately double up the excavation of the new 3’ slab with the backfilling of the frost wall in a week or two. This will at least ensure some efficiencies with excavation costs—having the site contractor cart his excavator out for a special trip to dig an extra 3’ would be wasteful.
Luckily, this was more of an emotional, not financial, stress. Yes, there will be added material and labor cost for building a 12’ vs 6’ bulkhead access. But at least we have to undo any work already completed. With a little foresight and collaboration, we were able to salvage the effort and material already invested.
Onwards!
ONE PICTURE
Concept for the development of two duplexes that doesn’t sacrifice on design.
📍 Pittsburg, PA
Source: The Hazelwood Initiative
That’s it for today. Thanks for reading. If you haven’t yet, go ahead and subscribe here:
About me: I’m Jonah Richard, a small-scale real estate developer in Vermont. With my company, Village Ventures, I’m currently getting my hands dirty developing Missing Middle housing.
Connect with me on LinkedIn.
Great photos. Is Clay Chapman a (distant) relative? Or just a coincidence?